In a sector often defined by fierce competition and rapid cycles, Karla Magruder, Founder and President of Accelerating Circularity, has built something quietly revolutionary: a system built on collaboration. With over 35 years of experience in the global textile industry—and a seat on advisory boards including the Cotton Board and Walmart Lighthouse—Magruder recognised early that the buzz around circularity needed grounding in infrastructure, not slogans.
“When Accelerating Circularity kicked off, it was obvious that people were starting to use the term 'circularity' as the next buzzword without understanding what it really meant to the textile industry,” said Magruder. “We believe that the industry needed access to correct information on what it means and how to go about developing systems to allow for circularity.”
Those systems are now becoming real. From its inception, Accelerating Circularity has focused on textile-to-textile recycling, with a stakeholder-led model that has attracted 74 partners across 21 countries. The organisation recently completed U.S. and EU trials that processed more than 72 tonnes of feedstock—textile waste diverted from landfill and used to create new materials that met both performance and restricted substance list (RSL) requirements.
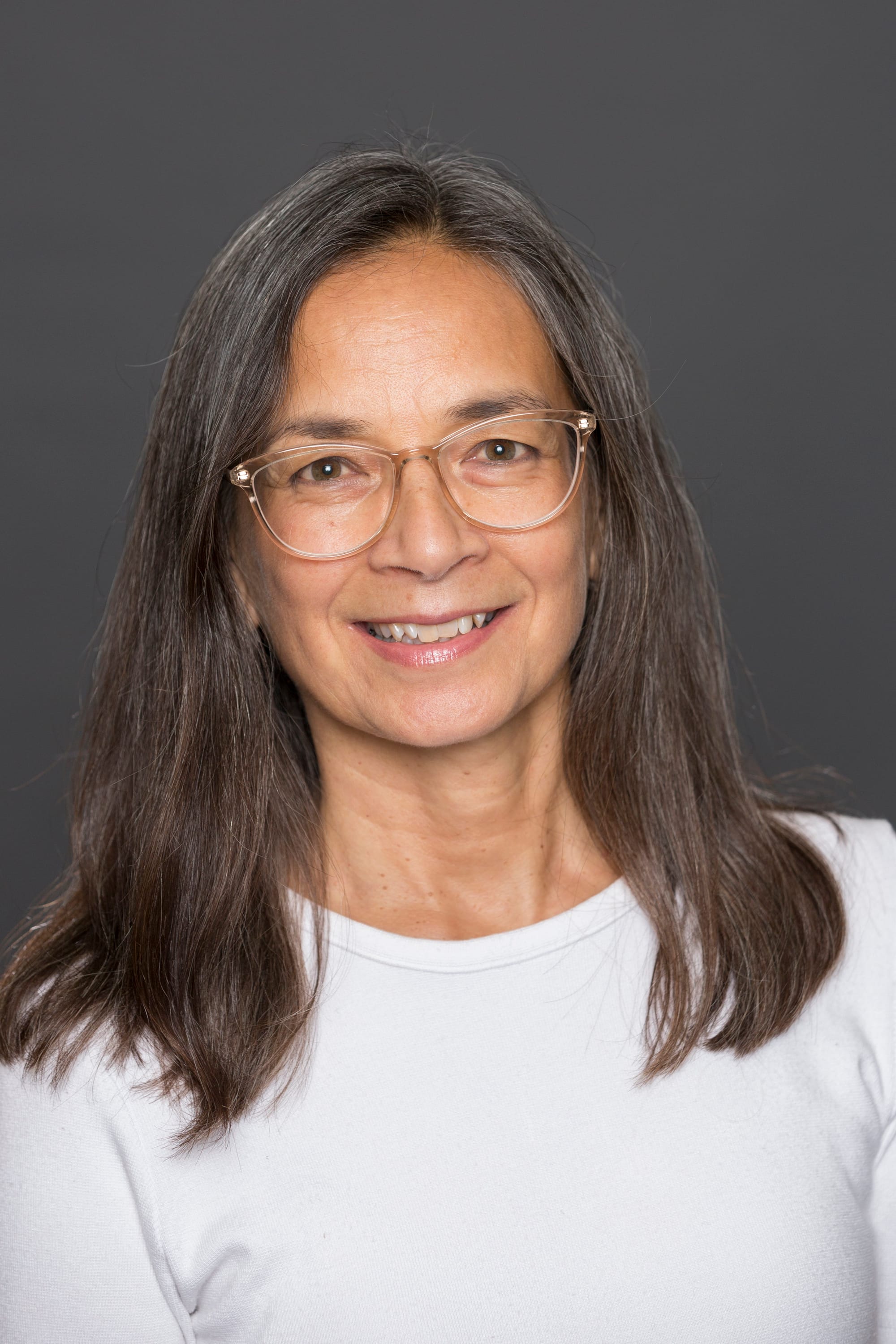
“The transition to circular systems is non-negotiable—collaboration is the only way we’ll make it work.”
- Karla Magruder, Founder and President of Accelerating Circularity
“The first and most important learning is that it's possible to incorporate post-consumer textiles into new raw materials that meet performance and RSL requirements,” said Magruder. “The second is there is still a lot of work to do to connect all the nodes.”
Those “nodes” refer to every component needed for a circular system to function—recyclers, collectors, brands, sorters, chemical processors, and more. For Magruder, systems thinking isn’t optional. “The keyword in your question is systems. For the system to function you're going to need collaboration—without it you can't connect all the parts.”
Accelerating Circularity’s "Building Circular Systems" initiative exemplifies this holistic approach. “We talk about being a stakeholder-led approach and that's how we work,” Magruder said. “We make sure that the voices of each node of the circular system brings their expertise to the programme.” By covering various types of recycling technologies, the initiative captures the full diversity of needs and outputs—an essential step in designing viable alternatives to linear models.
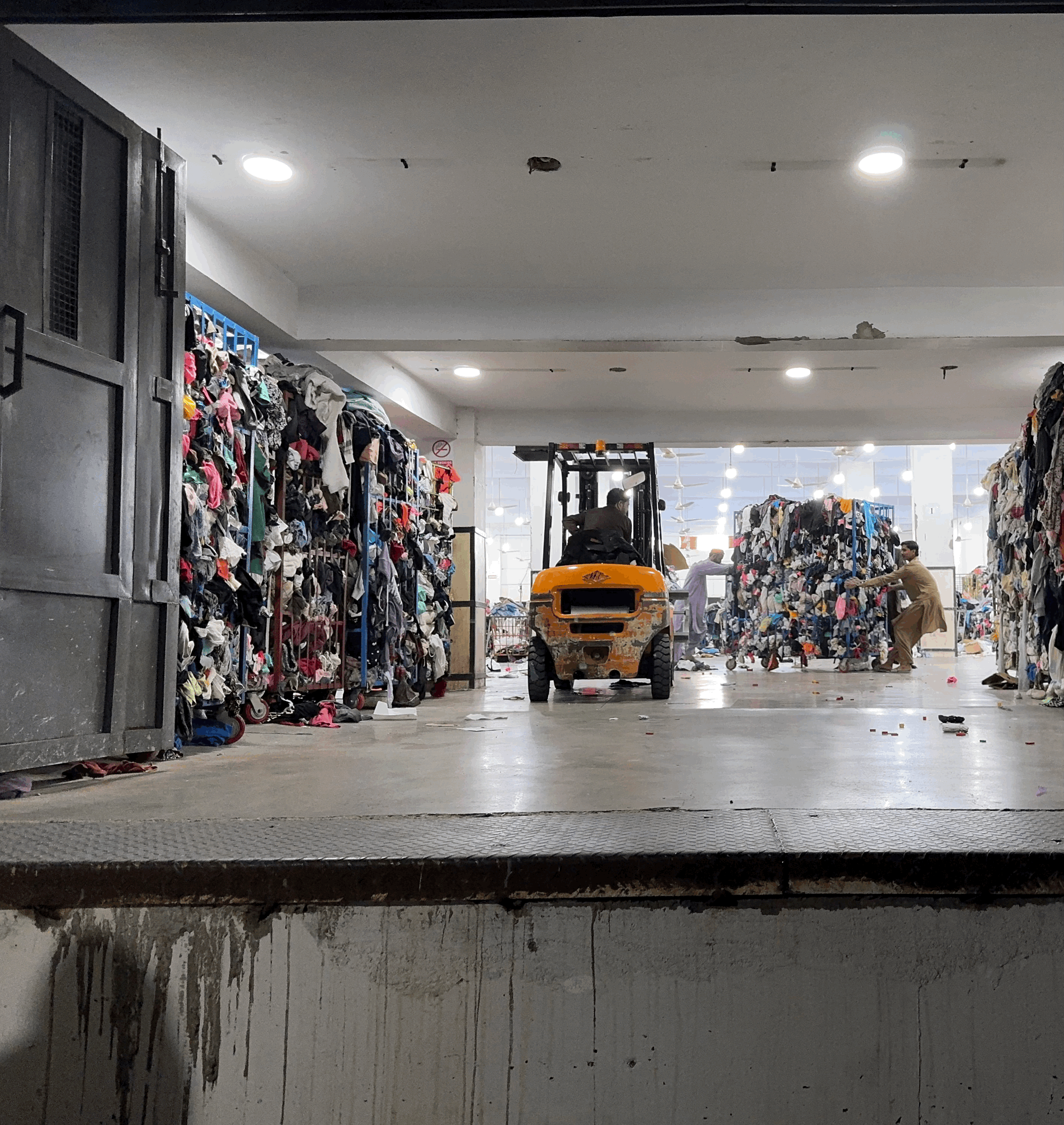
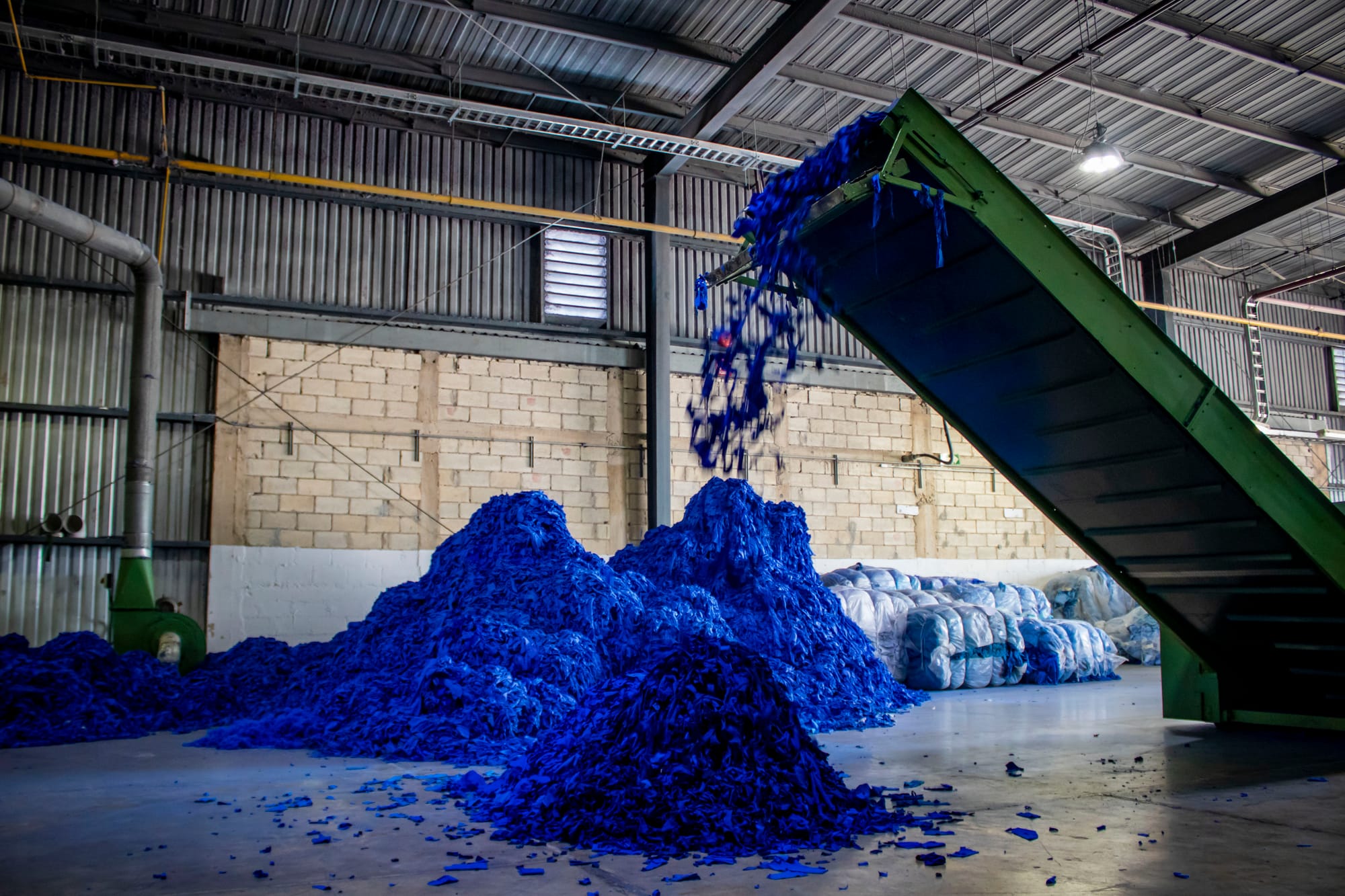
To support smarter decisions around textile waste, the organisation has also developed the Next Use Network Textile Hierarchy Tool. While still in early stages, the tool helps brands and manufacturers prioritise reuse and recycling pathways with measurable impact.
As for infrastructure—a common roadblock in circularity efforts—Magruder sees positive momentum. “It's amazing how quickly the missing infrastructure links are being addressed. Back to systems: without all the nodes functioning, circular systems are not going to work. Working collaboratively highlights the needs for the system which can then be addressed by the collective.”
Even challenges like garment trims, often made of mixed or non-recyclable materials, are being tackled head-on. “Trims are a real challenge,” she admitted. “The CSTIM working group works to understand the types of trims and how they might be handled in the new circular systems.”
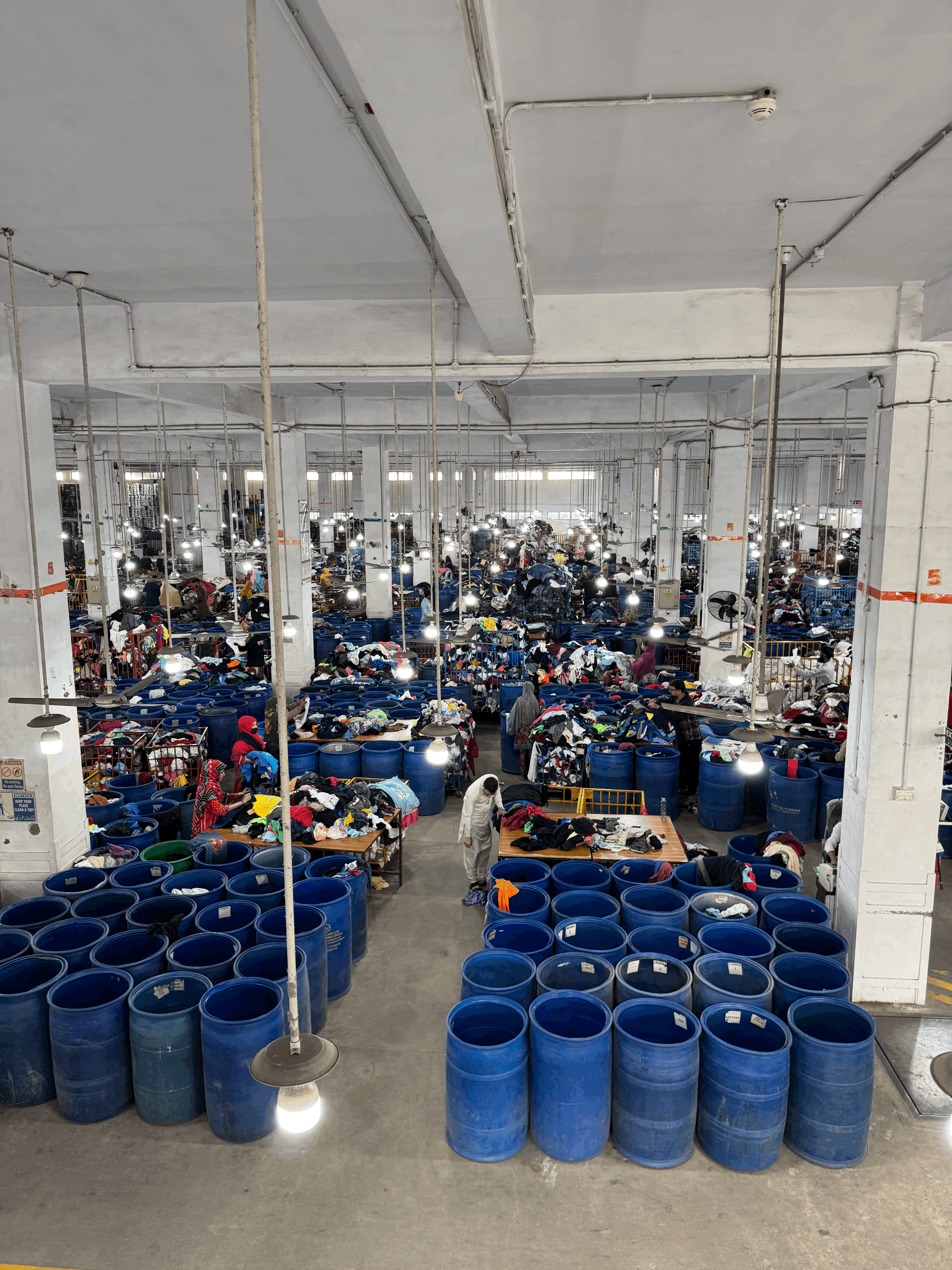
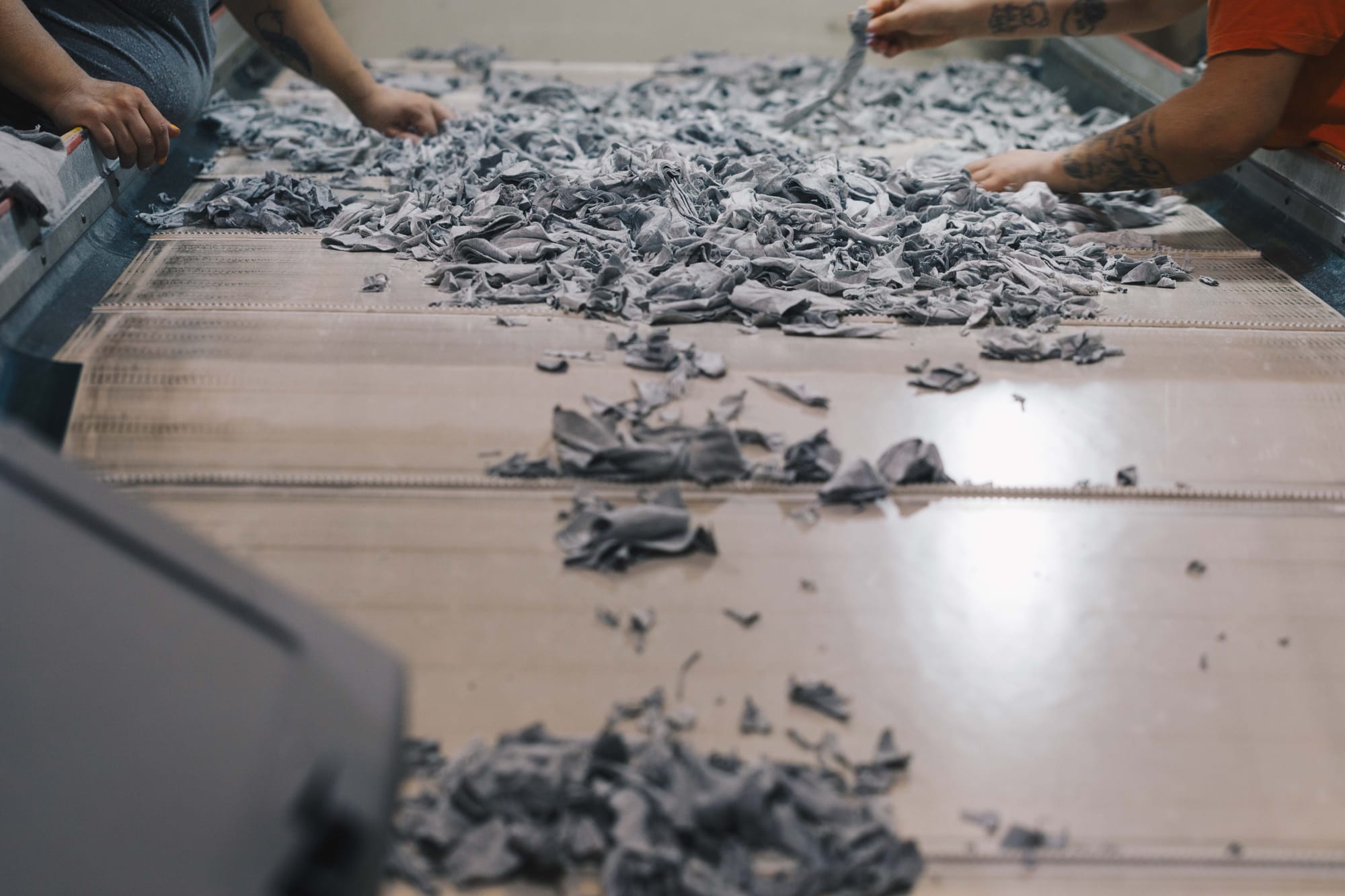
Notably, brands involved in Accelerating Circularity’s trials committed to using yarns and fabrics with a minimum of 40% recycled content. “There was agreement beforehand that we would shoot for a higher content. We were able to deliver on products containing 40% recycled as a proof of concept,” Magruder noted, with the caveat that future levels may vary depending on quality and price requirements.
Sorters and collectors, often overlooked in supply chain discussions, also have a seat at the table. “They provide their expertise on what is possible and where the challenges are,” said Magruder, reinforcing that successful circularity demands input from all corners of the industry.
The organisation’s commitment at the Clinton Global Initiative aims to process 325 tonnes of feedstock by 2026. “The expected impact is to send enough material through the system for it to be established. It’s important that the system can put production volumes through to validate and commercialise the process,” Magruder said.
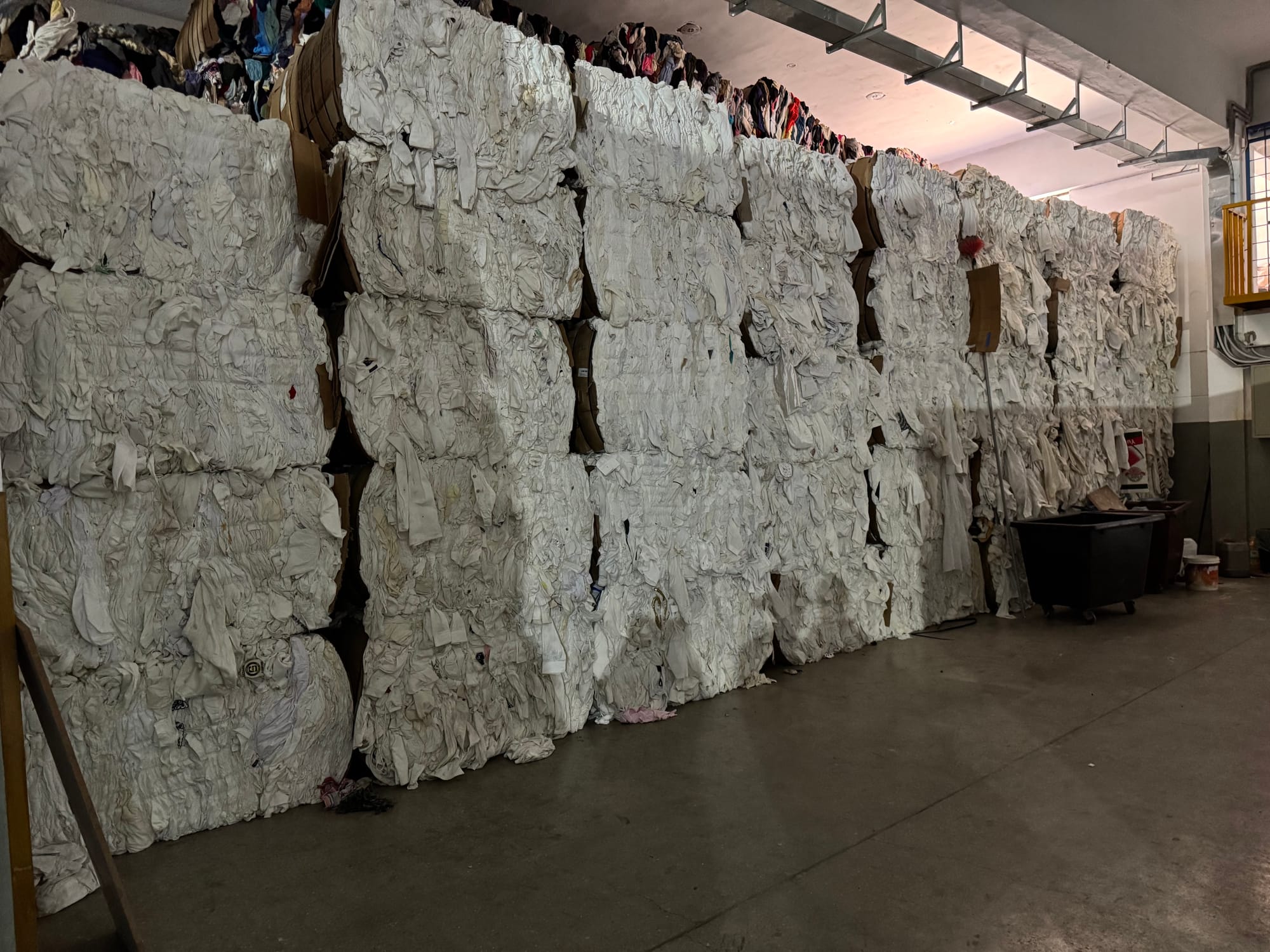
Ensuring scalability and commercial viability is baked into the model. “There’s a process for ensuring that a system is commercially viable by making sure that it flows through standard commercial systems from a performance, volume, logistics and quality point of view. Of course, the price is a big consideration.”
Despite the complexity of scaling across geographies and material streams, Accelerating Circularity is moving steadily ahead. While Magruder preferred to hold back details on future regions and recent funding, her optimism about the industry’s trajectory was clear.
“At Accelerating Circularity we know that the transition to circular systems is a non-negotiable,” she said. “We are inspired by the support from the industry for our work, as well as that of others, to make our organisation’s mission of ‘a world in which textiles are no longer wasted’ a reality.”
Through quiet, deliberate partnerships and hard-won learnings, that future is beginning to take shape.