In the world of design, where the boundaries between art, technology, and sustainability are constantly shifting, a new collaboration has emerged that exemplifies the future of fashion. Zulu Kuki, an innovative designer known for pushing the limits of the tangible and the virtual, has teamed up with Balena, a pioneer in biodegradable materials, to create a 3D-printed modular shoe that not only makes a visual statement but champions sustainability at its core.
For Kuki, the inspiration behind the design was a blend of his personal passions. “Automotive culture has been close to me for many years,” he explains. “I attend and organize events related to cars, and for some time, they’ve been a major source of inspiration in my work, including my 3D-printed shoes.” Drawing heavily from the sleek lines of 1970s racing cars, particularly the aerodynamic yet bold designs of Group 5 cars, Kuki's latest creation, the B_935 shoe, incorporates both curves and sharp, geometric lines to striking effect.
One of the standout features of the shoe is its modular design, an element inspired by the customizability of automobiles. Just as car enthusiasts can swap out parts to suit their preferences, Kuki envisioned shoes with interchangeable soles and socks. “I wanted to see how much of that car customisation could be transferred to shoes,” he says. "Customization allows you to adjust the shoe based on activity or personal style, and if a part wears out, you can replace it without buying an entirely new pair."
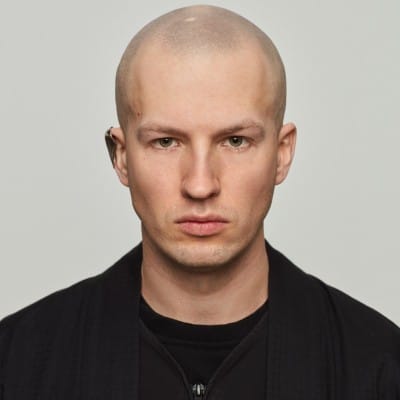
Innovative designer Zulu Kuki.
This level of innovation was made possible by the 3D printing technology Balena brought to the table, using their groundbreaking BioCir®flex3D material. Known for its flexibility, durability, and, crucially, biodegradability, this material enabled Kuki’s creative vision to become a reality. "3D printing is my bridge between the virtual and tangible worlds," Kuki notes, adding that while the technology has been around for years, it still offers vast potential for experimentation and innovation in fashion.
David Roubach, CEO of Balena, underscores the importance of their BioCir®flex3D material in this project. "BioCir®flex3D stands out from traditional 3D printing filaments due to its biodegradable properties and performance,” he says. “It’s both recyclable and industrially compostable, ensuring that when a product reaches the end of its life, it can be returned to the earth or recycled into new products.” This dual capability, Roubach explains, helps brands like Kuki’s reduce their environmental footprint while producing high-performance, customizable designs.
As the fashion industry moves towards sustainability, materials like BioCir®flex3D are essential to transforming the way designers think about production. According to Roubach, “BioCir®flex3D aligns perfectly with our mission to create a circular economy in fashion. With 3D printing, there’s less waste, and because the material can be composted or recycled, we’re not contributing to the landfill problem. It’s a win for both designers and the environment.”
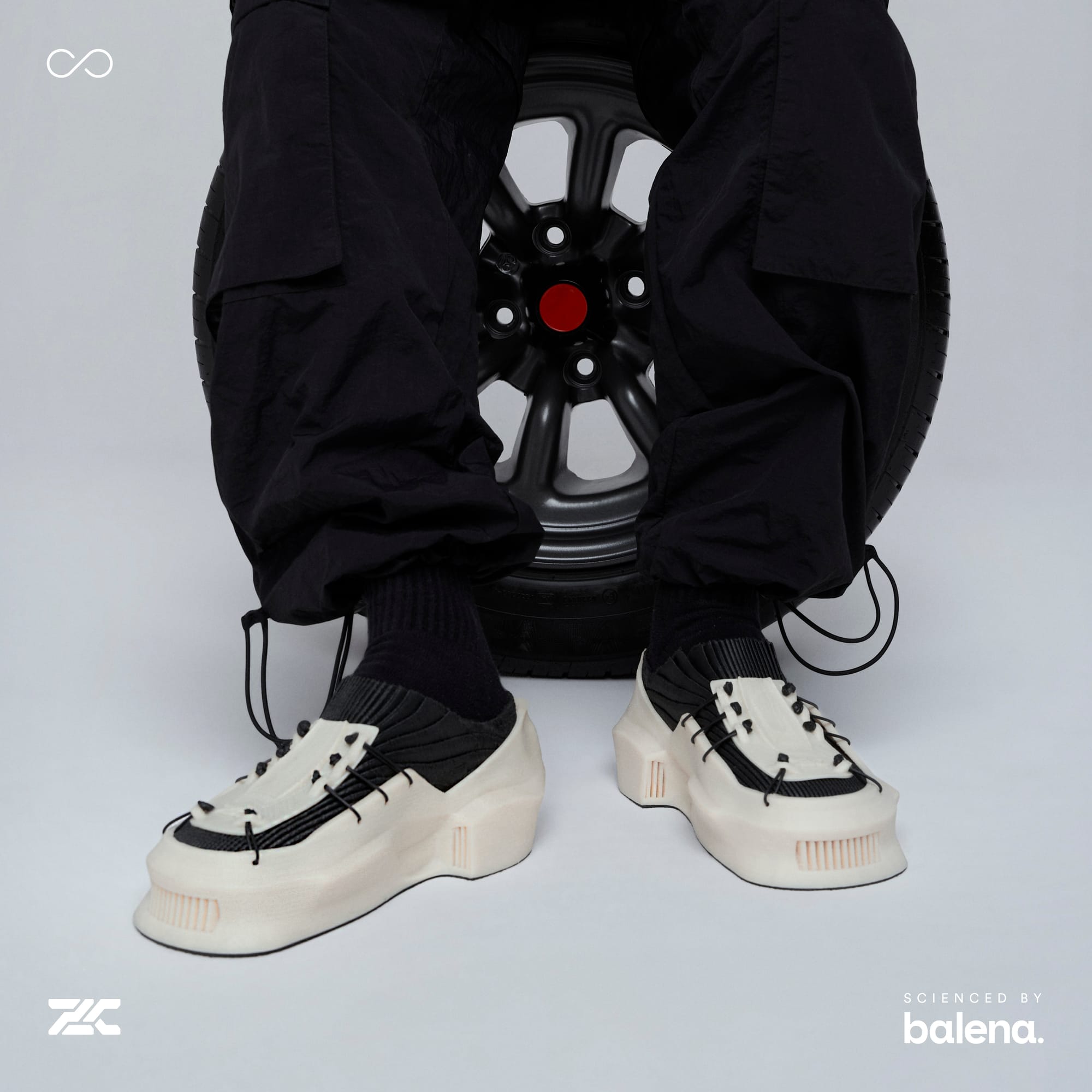
While this level of innovation sets new benchmarks in both fashion and sustainability, the collaboration wasn’t without its challenges. “The biggest obstacle,” Kuki admits, “was adapting the concept to the limitations of 3D printing.” Ensuring the different components of the shoe fit together seamlessly while retaining durability required careful consideration. "I designed a fastening system at the back of the shoe that holds the sock firmly in place when you walk, while the cage made from the same elastic filament ensures everything stays together." The result is a shoe that combines functional performance with a unique aesthetic, without compromising comfort or usability.
Modularity is more than just a design choice for Kuki; it’s a nod to the future of sustainable fashion. "The ability to swap out parts and repair sections of a shoe rather than disposing of the entire product is a game-changer,” he explains. By enabling consumers to replace worn-out elements, Kuki believes modularity will reduce waste and encourage a more mindful approach to consumption. “When a part of the shoe is no longer suitable, you can degrade it while the rest stays with you, eliminating the need for complete replacement.”

Beyond its practical benefits, Kuki’s design philosophy as a nomad—a constant explorer of new forms of expression—is reflected in this project. He views the collaboration with Balena as more than just a product launch; it’s a vision for the future of fashion. “I’d like to think of this project as a kind of scenario for the future of the fashion industry,” he says. "Projects like this partnership with Balena offer solutions that can introduce real change in the way we think about production and consumption."
Roubach echoes Kuki’s sentiments about the broader implications of their collaboration. "The global fashion industry is at a tipping point. As more designers and brands embrace materials like BioCir®flex3D, the industry will evolve toward more sustainable models, with waste minimised and creativity thriving." However, Roubach acknowledges that there are still barriers to overcome before circular materials can become mainstream. "Education and awareness are key, along with scaling production and improving the infrastructure for recycling and composting.”
Despite these challenges, the potential for 3D printing in footwear and fashion is immense. According to Roubach, the growing market for 3D-printed shoes is set to reach $6.3 billion by 2029, driven by consumer demand for customization and sustainability. Balena, with its innovative materials, is well-positioned to lead this charge. “We see BioCir®flex3D as a critical component of this future,” he says. "It allows brands to scale their production sustainably, without sacrificing performance or aesthetic value.”
For Kuki, this collaboration marks a milestone in his ever-evolving design journey. "I always put function first," he notes, adding that despite the shoe's striking appearance, it was designed with practical use in mind. "The sole, though visually massive, is flexible enough for walking, while the sock is designed for comfort and ventilation." The shoe’s bold departure from traditional aesthetics is a reflection of Kuki’s belief that fashion should embrace innovation without losing sight of usability.
As consumers increasingly seek out unique, customizable products that reflect their personal style and values, Kuki’s 3D-printed shoe stands at the intersection of innovation and sustainability. By harnessing the power of 3D printing and biodegradable materials, Kuki and Balena are setting a new standard for what’s possible in fashion.
Looking ahead, both Kuki and Roubach are optimistic about the future of 3D printing and biobased materials in fashion. "We have exciting projects in the pipeline that will continue to push the boundaries of what’s possible," says Roubach, hinting at further collaborations. "The possibilities are limitless when designers and material scientists work together to drive innovation."
In a world increasingly conscious of its environmental footprint, this collaboration between Zulu Kuki and Balena represents a bold step forward. By merging groundbreaking design with sustainable technology, they are not just creating a shoe—they are shaping the future of fashion.