The 3D printing industry is evolving rapidly, pushing the boundaries of what is possible with design, customization, and production. Yet, with growth comes a rising demand for more sustainable practices, especially when it comes to materials. Balena, a pioneering material science company, has responded to this challenge with the creation of Balena.Filaflex—a groundbreaking filament that combines sustainability with high-performance capabilities. This innovative product is the result of a new partnership with Recreus, a leader in flexible 3D printing filaments.
David Roubach, CEO of Balena, reflects on how this partnership with Recreus came about. "From the start, our goal has always been to merge sustainability with performance in the 3D printing space. We noticed that many of the materials used in the market, like TPU and PLA, were falling short on either flexibility or end-of-life solutions. That's where our BioCir®flex3D material came in—it's a biobased, fully circular filament that balances flexibility, durability, and sustainability. When we connected with Recreus, a company that shares our vision for a more sustainable future, it felt like the perfect synergy."
Balena.Filaflex is unique for its ability to offer a high-performance alternative to traditional filaments. Its key attributes include flexibility, durability, and a fully circular lifecycle that includes being biobased, recyclable, and compostable. "Balena.Filaflex delivers a rubber-like flexibility that is ideal for applications in industries such as fashion, footwear, and consumer goods," Roubach explains. "It’s a product that can withstand the rigours of daily use while being environmentally responsible. Unlike conventional filaments, which often end up in landfills, Balena.Filaflex offers a path to a more sustainable future."
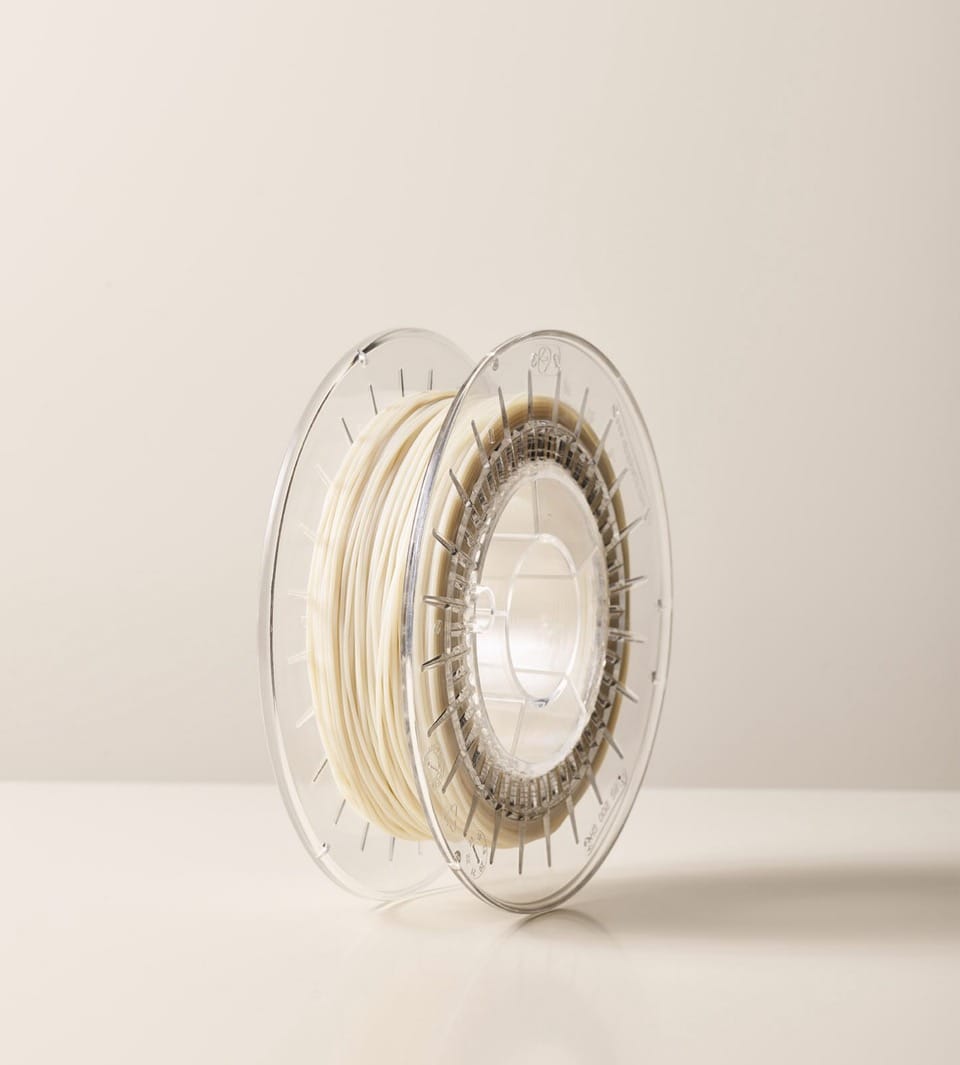
For a product like Balena.Filaflex to truly make a mark, the right platform for launch was essential. Enter Formnext 2024—the premier global event for additive manufacturing. “Formnext is the perfect stage to introduce Balena.Filaflex to the world,” says Roubach. “This is where innovation meets industry, and it’s the ideal space to showcase how sustainability and high performance can come together in a 3D printing material. The event attracts professionals from across sectors like aerospace, automotive, and fashion—industries that stand to benefit from a sustainable yet high-performance filament.”
As the 3D printing sector is projected to reach $48.67 billion by 2030, the demand for sustainable materials has never been more critical. "Consumers and regulators alike are demanding more from manufacturers. Biobased, compostable materials like Balena.Filaflex are not just an innovation—they are an imperative," says Roubach. "In an industry that is set to expand dramatically, there is a need to address the environmental concerns associated with the plastics used in 3D printing. By offering a solution that is biobased and has a fully circular lifecycle, Balena.Filaflex is positioned to play a key role in this transition."
The partnership with Recreus takes this vision a step further, combining Balena’s material science expertise with Recreus's reputation in the flexible filament market. "Recreus has a long-standing presence in the industry, and their Filaflex line has set a standard for flexibility. By combining this expertise with our BioCir®flex3D material, we’ve created a filament that offers both performance and sustainability," Roubach says. "Through this collaboration, we aim to bring more sustainable materials to the forefront of the 3D printing community."
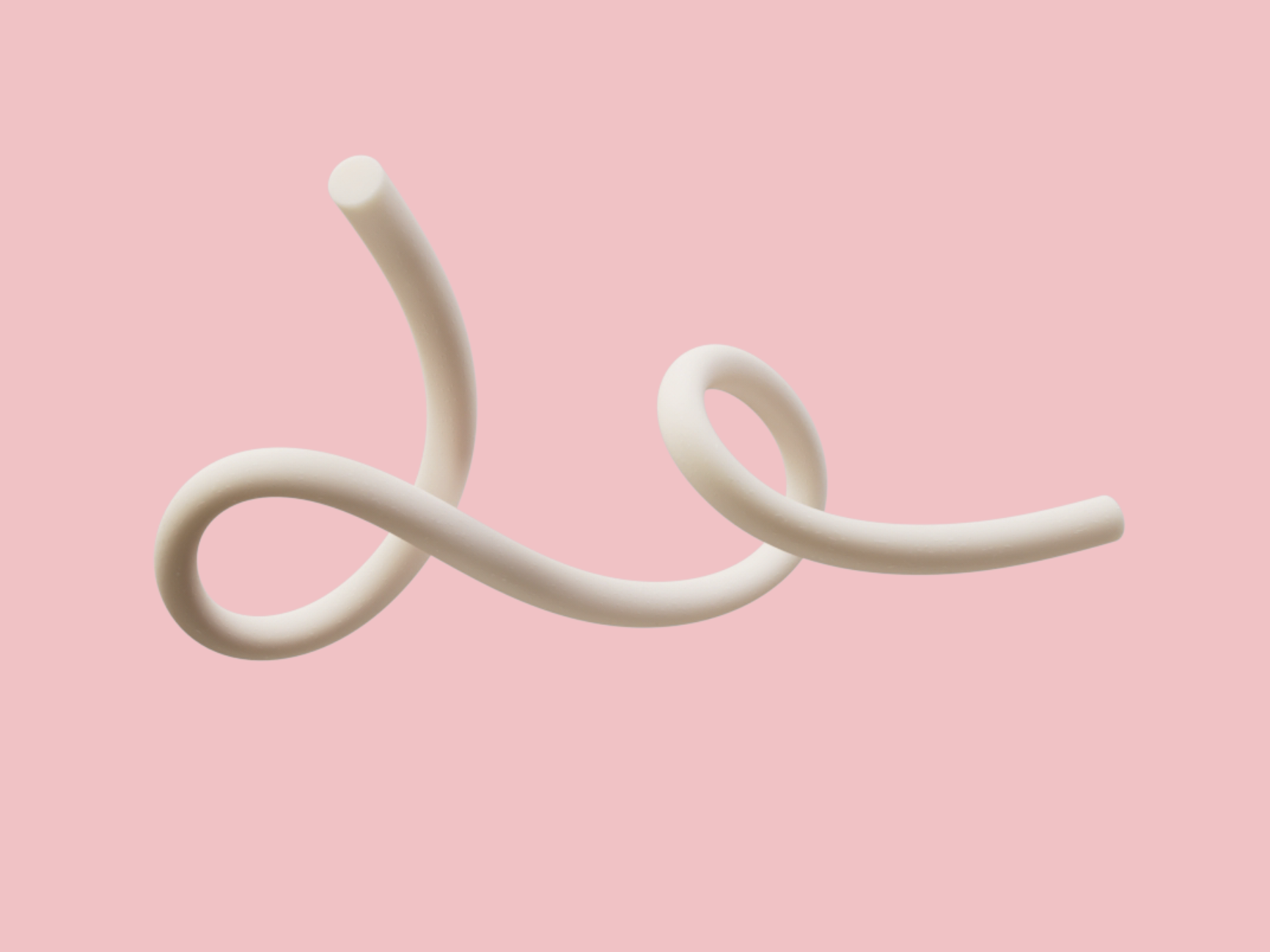
But the road to creating a sustainable filament wasn’t without its challenges. "Creating a material that is both biodegradable and high-performance is not easy," admits Roubach. "Thermoplastic polyurethane (TPU) is known for its flexibility and durability, but it lacks sustainability. On the other hand, PLA is compostable but falls short in performance, especially in high-stress applications. The real breakthrough came when we developed BioCir®flex3D, which bridges this gap—offering a material that’s as strong and flexible as traditional plastics but with a much lower environmental impact."
For designers and innovators, the introduction of Balena.Filaflex opens up exciting new possibilities. "One of the most significant benefits of Balena.Filaflex is its versatility," Roubach continues. "Designers can now create intricate, high-performance products while also aligning with sustainability goals. Whether in fashion, footwear, or consumer goods, Balena.Filaflex offers a new opportunity to create products that are not only flexible and durable but also contribute to a circular economy."
The growing need for biodegradable and recyclable materials in 3D printing is part of a wider movement towards more sustainable manufacturing. "As industries face increased pressure to reduce their environmental footprints, Balena.Filaflex is a step in the right direction. It meets the growing demand for products that can be composted or recycled at the end of their life," says Roubach. "This is not just about creating a better material—it’s about creating a better way to manufacture."
Looking to the future, Roubach is optimistic about the role that sustainable materials like Balena.Filaflex will play in shaping the industry. "Our vision is to make sustainable, circular materials the standard in 3D printing," he says. "Through our partnership with Recreus, we’re not just providing a new filament. We’re helping to lay the foundation for a more sustainable future in manufacturing—one where high-performance materials are designed with the full lifecycle in mind."
The collaboration between Balena and Recreus marks a significant milestone in the journey toward more sustainable 3D printing. As the global demand for eco-friendly materials continues to rise, innovations like Balena.Filaflex are poised to lead the way in transforming industries, from fashion to footwear, and beyond. The future of 3D printing is bright, and with partnerships like this, it’s clear that sustainability and performance can go hand in hand.